May 25, 2014
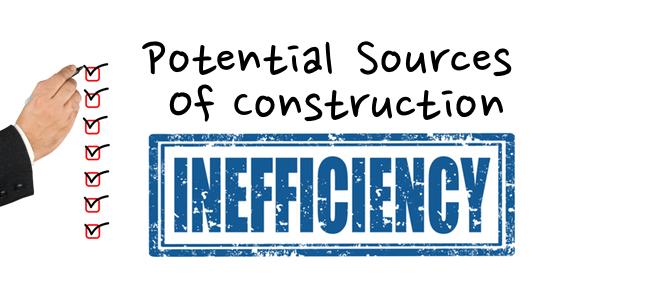
Let’s talk about the potential sources of inefficiency. There are many. They can include, but are not limited to:
- Extended periods of overtime
- Unanticipated inclement weather
- Revised means or methods instituted to overcome a delay (owner or contractor caused)
- The experience (also called learning) curve of each operation, you don’t always achieve the planned level of productivity on day one
- Equipment breakdowns
- Additional shifts (requiring additional labor and, potentially, additional management and coordination)
- The number, magnitude, and timing of changes
- Labor shortages (the contractor might be unable to obtain the required level of skilled labor)
- Poor management
- Site conditions and site access (differing site conditions or lack of access to the project)
- Increase or decrease in crew size
- Site organization or access (a contractor’s productivity may be reduced because the owner did not provide the contractor with access to the project site as stated in the contract)
- Trade stacking
- Erroneous or ambiguous drawings or specifications
- Rework
- Out-of-sequence work
As you can see, there are many potential factors that could cause the contractor’s operation to be less efficient.
When we talk about inefficiency, the party responsible could be the owner, the contractor, or a third party. Therefore, understanding the reason for the contractor’s lost productivity and the party responsible determines whether the contractor will be entitled to additional compensation for the inefficient operation.
Mark Nagata is a Director/Shareholder of TRAUNER and is an expert in the areas of critical path method scheduling, delay
April 27, 2014
![[Construction inefficiency first post]](https://www.traunerconsulting.com/wp-content/uploads/Construction-Inefficiency-Post-One-Header-version-two.jpg)
More and more of the construction claims that we review, evaluate, or prepare include a lost productivity or inefficiency component.
What is Inefficiency?
When a contractor alleges that one of its operations is inefficient, it typically means that the contractor did not achieve his or her anticipated level of productivity and, thus, incurred increased costs in the performance of that work item.
Why is a Contractor’s Planned Level of Productivity an Essential Part of its Bid Price?
Well, productivity on construction projects became a concern the instant contractors became interested in making a profit, which is probably right after the shovel was invented.
It really comes down to this. When a contractor submits its bid, its price is based on achieving a particular level of productivity on each of the work packages that comprise the entire project. The contractor’s ability to achieve or exceed that level of productivity has a significant impact on its profit margin/bottom line.
For example, if an item of work is not completed within budget, then one of the reasons for the increased cost could be that the contractor did not achieve its planned level of productivity. This lost productivity or inefficiency is caused by expending more labor or equipment hours than planned to complete the work item. This expenditure of additional hours can lead to real, significant, and unanticipated increased costs.
As projects have become more complex, the potential for experiencing
February 09, 2014
![[Substantial Completion…The Haze at the End of the Tunnel] [substantial Completion]](https://www.traunerconsulting.com/wp-content/uploads/Substantial_Completion_Haze.jpg)
The Notice to Proceed clearly marks the start of construction. If nothing else, it determines when the clock starts ticking, counting off the time to the contract completion date. At the other end of the project, however, the demarcation is often not so clear, resembling more haze than light at the end of the tunnel.
The construction start date is easier to determine and more clearly defined because it is measured objectively. On most projects, the contract states that the project start date is the Notice to Proceed date. At the other end of the tunnel, however, most contracts rely upon a subjective evaluation to determine the project’s completion. Couple this subjectivity with the ways of defining completion and the source of the haze becomes apparent.
What Is Substantial Completion?
Usually, completion is defined two ways. The first measure is substantial completion. AIA Document A201 defines this phase as follows:
9.8 SUBSTANTIAL COMPLETION
9.8.1 Substantial Completion is the stage in the progress of Work when the Work or
designated portion thereof is sufficiently complete in accordance with the
Contract Documents so the Owner can occupy or utilize the Work for its
intended use.
Note the words “sufficiently complete”. On many projects, sufficiently complete cannot be defined objectively. It cannot be measured with a yard stick. It is not usually identified by the completion of a single activity or
January 12, 2014
In the last Ideas & Insights, we discussed field and home office overhead and gave you some overhead cost examples. I think the next question is, well, how does a contractor bid these costs? How do they include these costs in their contract?
Home office costs are often bid as a percentage. If you were looking at a contractor’s bid, that percentage might be called G & A, “General and Administrative, or G, A, & M, “Administrative and Marketing.” It’s a markup percentage, or maybe a lump sum amount, that is applied to the contractor’s bid price to account for the amount of money that this project needs to generate in terms of revenue to help cover the costs of the home office.
Field office overhead costs are usually bid quite differently. They’re usually estimated, like any cost, and included in the overall price of the project based on that estimated cost. The estimator figures out how may project engineers they’re going to need and how many superintendents they’re going to need and how many non-working foremen they’re going to need. They figure out what their likely salaries are and they multiply by the number of hours or amount of time they’re going to be on the project. That becomes their estimated price for project managers and superintendents and non-working foremen. They do the same for the trailer. They do the same for Porta-Johns. At the end of the day, a contractor has priced, by estimating, what they think field office
December 15, 2013
![[What Types of Overhead Costs Could A Contractor Include In A Construction Claim?] [Funnel Graphic]](https://www.traunerconsulting.com/wp-content/uploads/funnel1.jpg)
Let’s talk a little bit about two types of overhead costs contractors might include in construction claims.
Field Office Overhead Costs
The first is field office overhead. We probably all easily recognize what field office overhead is. They are the costs the contractor incurs to maintain operations in the field, but typically they’re not costs associated with any one item of work.
Good examples of this would be the field office, the trailer, and if the contractor is renting a field trailer or office space specifically for a project. This field office cost isn’t associated with any particular item of work. You can’t attribute it only to concrete work or excavation or even drywall installation.
In order to efficiently manage the work, however, you must have a field office. You need a place to put your project manager and your project engineer and their clerical support. The field office is a common field office overhead cost, or site overhead cost.
Utilities to support that office and the performance of work are other examples. Let’s not forget the project managers themselves, the superintendents, the Porta-Johns, the computers, the paper, and all of the things that we need to maintain an office and presence in the field. None of these things are specifically associated with any particular item of work. Thus, they really aren’t paid for when we compensate the contractor for
November 17, 2013
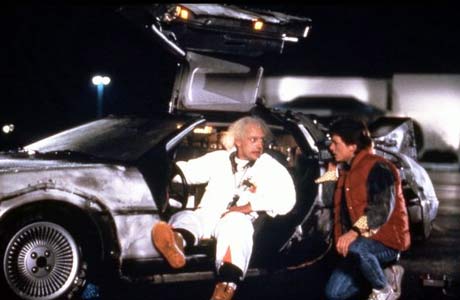
Hint: It doesn’t involve a Delorean!
You should use the time impact analysis approach I wrote about in the last Ideas & Insights as a technique to measure delays that haven’t occurred yet. You are contemplating a change. You haven’t actually executed the change. The contractor hasn’t performed the change work. You’re just trying to figure out if that change might delay the project. It would be part of the change, or the proposal, or change order request.
What do you do if the project has already been delayed? What if you’re looking in hindsight? Like, for example, say you’ve experienced a weather-related delay in construction like one that Superstorm Sandy may have caused in late October 2012. Use a contemporaneous analysis when evaluating delays that have already occurred.
A contemporaneous analysis is exactly what it sounds like. It’s an evaluation of the contemporaneous project schedules, tracking the critical path from update to update, identifying each and every critical delay, and thus being able to identify how something like Sandy may have affected your project. That’s a contemporaneous analysis.
You don’t analyze delays in a contemporaneous analysis by modifying the schedule. When doing a contemporaneous analysis, you analyze delays by looking at the history of the project and how the project work is unfolding. You’re tracking the critical path.
Let me give you an example. Let’s say excavation
October 20, 2013
Scott Explains Time Impact Analysis in this YouTube video
Time Impact Analysis (TIA) is a common approach to analyzing delays on a project. You develop a fragnet, which is a fragmentary network for the issue (i.e. the change). It’s like a little mini-schedule for the change. You take that fragmentary network, you drop it into contemporaneous schedule, and then look to see how it affects that schedule. That’s the TIA analysis.
If you’re looking at delays prospectively, in other words, before they’ve occurred (you’ve got a change and you’re trying to figure out how this change you’re contemplating would affect the project) a TIA approach is the approach you’d use to evaluate the delay. Use the TIA to identify and measure critical delays that have not yet occurred.
This is the approach you use before the delay has occurred. Unless required by the contract, do not use this method to evaluate delays that have already occurred. Don’t use it to look behind you.
We’re not going to go through the step-by-step of the TIA. That’s beyond the scope of this particular Ideas & Insights. If you’re interested in knowing the steps, just send me an email at scott.lowe@traunerconsulting.com.
One other thing, if you’re looking for a source that describes probably the closest thing that exists to an industry-wide standard with regard to how you would conduct a TIA analysis, I could point to the Recommended Practice for Forensic Schedule Analysis. This document is published by an organization called the Association for the
September 22, 2013
![[What Do You Do If the CM Micromanages The Contract’s Schedule and Withholds Approval?] [Angry Construction Worker]](https://www.traunerconsulting.com/wp-content/uploads/CMYelling.jpg)
Here’s a question. What do you do if the Construction Manager micromanages the contractor’s schedule and withholds approval so the project proceeds for months without a schedule and, as a consequence, the contractor has their own in-house schedule that is different? Can the contractor use their in-house schedule as a basis for measuring the delay?
The short answer to this question, in my opinion, is yes. Ultimately, the right answer is whichever schedule is best. In other words, if the CM’s position is that the schedule is tragically flawed, and the reason for their rejection of the schedule was this tragic flaw, and because of this flaw the schedule is not an accurate representation of the contractor’s plan for completing the work, the CM has a point.
I often say, at least to my staff, use the contemporaneous project schedules to measure delay, but don’t hold tight to those schedules and jump off a cliff with them. The point I’m trying to make is that nobody believes the right way to measure a delay is to use a schedule that is truly, deeply flawed.
I think if the contractor has developed a workable, reasonable, sensible schedule that truly and honestly sets forth the contractor’s plan for executing the project, the contractor keeps that schedule updated, and the contractor
August 19, 2013
![[A New Website on Delay Damages] [delay damages website]](https://www.traunerconsulting.com/wp-content/uploads/Delay_Damages_header.png)
Sometimes we want to share more information than could fit into an Ideas and Insights. With that in mind, we created DelayDamages.com. We hope to grow this new website into the most comprehensive resource on the topic of construction delay damages.
The website already has a lot of information on the following topics:
We’d love to hear your thoughts on this new website. Send an email to <mark.nagata@traunerconsulting.com> to let us know what you think or ask any questions about the topic. We look forward to hearing from you.
February 24, 2013
One reason why you want to give time extensions when time extensions are due is you don’t want to develop a situation where the contractor is entitled to a time extension, but the owner is refusing to provide one.
This can lead to a type of acceleration called, “constructive acceleration.” “Constructive” in this case meaning, “in effect.” Essentially, it’s an acceleration that is the result of the actions or behaviors of the parties. It would be in contrast, for example, to a directed acceleration.
In order to prove construction acceleration, the contractor must demonstrate five things:
The contractor has experienced what’s called an, “excusable delay.” An excusable delay is a delay for which the contractor is entitled to a time extension, usually a critical delay that’s not the fault and responsibility of the contractor.
The contractor then requests a time extension for that excusable delay.
The owner rejects or is silent as to whether a time extension will be provided. Because the contractor is not getting additional time to complete the work, the contractor is now concerned that they might be assessed liquidated damages. Or worse yet, that the owner might conclude that they are in fact in breach of the contract. Or the owner directs the contractor to finish the project by the original contract date without an extension.
The contractor, for that reason, gives notice to the owner that it will have to accelerate it’s work in order to finish the project by the